Board to Board Connectors in medical technology
The right contacts in medical technology
In the medical technology sector networked medtech devices with an increasing number of smart sensors will dominate the scene. The strictest regulations and the highest level of failure protection set the path that the products and components used must follow. Miniaturization, data transfer rates and electromagnetic radiation are the explicit requirements to which board-to-board connectors are exposed. For hardware developers these are criteria that have a decisive influence on device design.Today patients still have to adapt to the structures of the healthcare system. Tomorrow – and Deloitte's forecasts apply to 2025 – healthcare will be oriented in exactly the opposite direction, towards patients, their location and their time constraints. The move towards this "4P medicine" (predictive, preventative, personalized, participatory) will be facilitated by many digital innovations.
This paradigm shift will be reflected in the manufacturers of medical devices. The number of smart sensors is increasing with the networking of products in the Internet of Medical Things (IoMT). In patient care, convenience is increasing, for example through wireless connections to electronic patient records and the transmission and monitoring of vital parameters in real time. Data analytics, cognitive methods and robotics are opening up further areas of potential in the healthcare sector.
Highspeed and EMV in the focus of medical devices
Medical imaging systems such as CT scanners, MRI devices and digital X-ray machines process up to 20 Gbit/s of image and patient data in real time. The same applies to telemedicine and remote monitoring applications. Surgical robotics also require the real-time transmission of images and control commands between the surgeon's console and the robotic system. High-resolution endoscopy, implantable devices and patient monitoring systems are other fields that rely on data transmission, but also place importance on EMC design aspects for interference immunity and patient safety.Other trends such as the increase in multi-source sensor technology and increasingly networked overall systems require fast, reliable and secure data transmission via various interfaces - a fact that applies in particular to MedTech devices. Signal integrity plays a decisive role here, with high-precision and reliable data predominating in the applications. Constant currents and accurate data are essential to ensure the functional safety, reliability and efficiency of the devices. High bit rates, sometimes over long distances, can affect electrical signals to such an extent that errors occur and devices fail due to interference such as noise, (feedback) coupling losses, distortion and crosstalk.
Compliance with relevant industry standards
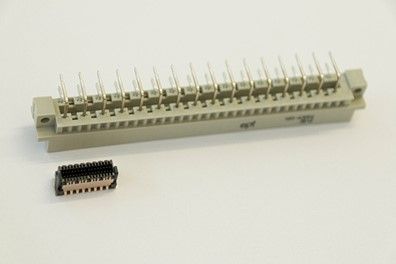
Fig. 2: An old D-series DIN connector with a 5.08 mm pitch and the new Zero8 with a 0.8 mm pitch below it
In the context of regulatory requirements such as the Medical Device Regulation (MDR) in the European Union or the Food and Drug Administration (FDA) regulations in the USA, it is important to ensure the approval and safe use of devices. The trend among all hardware designers is also to make even more efficient use of the ever-shrinking installation space in medical devices, whereby the stresses on the devices in terms of shock, vibration and oscillation, as well as thermal and chemical environmental influences, continue to demand the robustness of all devices.
Furthermore, there are three focused, application-specific industry standards for MedTech devices that must be taken into account in all designs. Firstly, ISO 80369-1, which deals with the design methodology to reduce the risk of misconnection of medical devices or accessories. Secondly, IEC 60601, which describes the general requirements for basic safety and essential performance, including electromagnetic interference (EMI) and electromagnetic compatibility (EMC). And thirdly, ISO 13485, which refers to the quality systems responsible for the traceability of components and procedures used in the production process.
Board-to-Board connectors as signal transmitters
If the complexity and integration density in medical devices continues to increase and existing and new functionalities have to be integrated in the smallest of spaces, then the demands on board-to-board connectors as a bridge between the circuit boards are immensely high. A wide variety of locations and areas of use subject the devices to vibrations and shocks. The connectors must ensure long-term contact reliability during micromovements. Robustness, data transmission and EMC shielding are the three cornerstones of mechanical device design for the hardware developer.The latest generation of connectors must minimize interference in signal transmission and the contact design of the connectors must be perfectly matched to this. The aim is therefore always to avoid the risks in data transmission, which mainly include fluctuations in impedance due to changes in material and geometry, attenuation due to insertion loss and return loss as well as crosstalk.
Signal protection as a basis
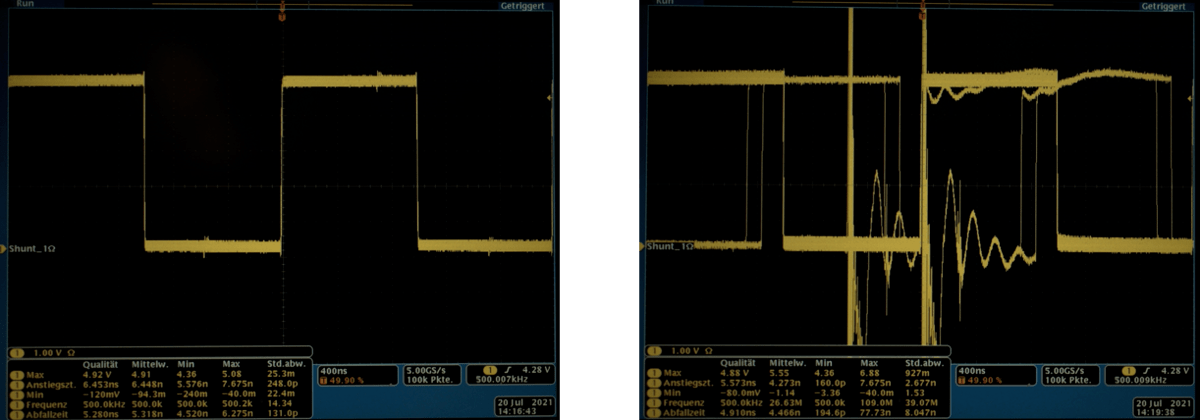
Fig. 3: Interference on the signal with shielded (left) and unshielded (right) connectors.
With regard to electromagnetic influences, high-speed signals require special signal protection. A connector can act both as a source of interference and as a sink. Signal protection using a shielding plate is recommended here to protect the sensitive signals from external influences. Figure 3 shows that even a small electrical impulse can distort the useful signal.
The receiver can no longer clearly interpret the digital states of the HDMI signal even after a short burst pulse of 0.5 kV, whereas the signal transmission of the shielded connector is still stable even at 4.4 kV.
The coupling inductance LK describes the connector by the electrical ratios in both functions - source and sink. This applies to both interference immunity and interference emission. If the induced voltage (Uind), the voltage of the generator (UGen) and the generator constant (kGen) are known, the specific maximum permissible coupling inductance (LK) can be determined using this equation:
LK = Uind / (UGen * kGen) (Eq. 1)
The coupling inductance also helps the user to define the appropriate connector in terms of its electromagnetic compatibility and to avoid costly and time-consuming trial-and-error tests in the EMC laboratory. Here is an example: A case-specific maximum coupling inductance of 47 pH was determined for an HDMI signal at a voltage of 4.4 kV. If the value is higher than this, the signal is no longer transmitted without interference.
Especially for demanding industrial applications
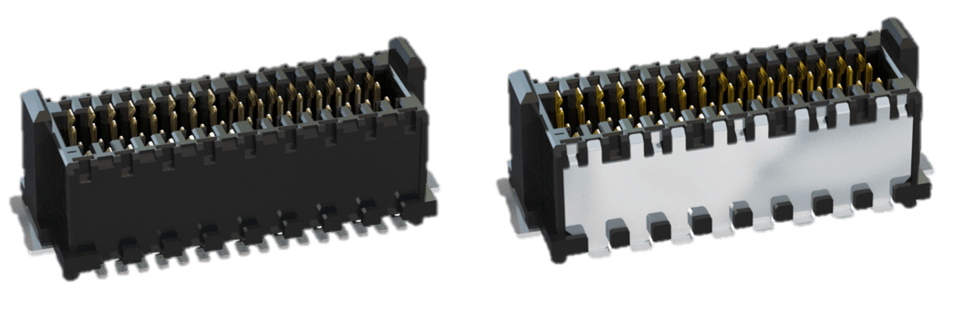
Fig. 4: Zero8 in unshielded (left) and shielded (right) version
The Zero8 product family from ept has been designed for these high demands in medical technology and, with its high scalability, offers ideal adaptation to individual requirements - designs, stacking height and number of poles can be selected individually. Sockets and connectors are currently available in mid-profile and low-profile designs and will also be available in high-profile and angled versions in the future. Thanks to the different heights, Zero8 connectors can be used to realize PCB spacings from 6.00 mm to 21.00 mm, with the number of poles varying between 12 and 80. For shielding purposes, both sides of the connector pair can be selected with protection, whereby all Zero8 connectors are of course compatible with each other and can be freely combined.
The ScaleX double-sided connection technology can withstand the harsh conditions of industrial applications and ensures reliable contacting under mechanical stress such as shock and vibration. It also compensates for device-side tolerances in all directions when mated. The EMC shielding protects the signals from external influences in industrial environments and the material properties guarantee a data transmission rate of up to 16 Gbit/s.
Source: EPT - Board to Board Connectors in medical technology (ept-connectors.com)